By Shavantay Minnis
Imagine being afraid to pick up your grandchild. That’s the reality for some amputees when they can’t control the strength of their grip because they can’t feel it, said Erik Engeberg, Ph.D., professor in the College of Engineering and
Computer Science.
But Engeberg’s recent research just might change all that.
Prosthetics are useful, he said, but they lack touch, which means amputees have less information about the world around them. Improving robotic parts that allow individuals to regain sensation and ultimately feel the sensation of touch is the goal, said Engeberg, who is also the director of the BioRobotics Lab at FAU, member in the FAU Stiles-Nicholson Brain Institute, fellow in the FAU Institute for Sensing and Embedded Network Systems Engineering and the FAU Center for Complex Systems and Brain Sciences.
For his work on prosthetics, he uses liquid metal sensors on artificial intelligent (AI) fingertips to provide a more realistic experience by creating an advanced sensation of touch. Using custom fabricated fingertips for a prosthetic hand, Engeberg inserts a liquid metal sensor on each fingertip to collect individual sensory data that can eventually send signals to the entire hand, so it senses what it’s touching.
“Imagine using an individual finger to feel a keyboard or a mouse. The ridges on the keys, or the wheel of the mouse, signals your hands and it can then automatically determine what it’s touching,” Engeberg said. “A prosthetic hand should be
no different.”
With four different corduroy style textures, each with a different distance between the ridges of the texture, and with a different speed set, the artificial fingers learn how to determine complex multi-textured surfaces. The sensors attached to the fingertips send information to a computer software system that trained machine learning algorithms to predict a recognized pattern of textures,
he said.
Engeberg also developed a system that merges live nerve tissue with a robotic prosthesis to create a living robotic hand — a multidisciplinary project funded by National Institutes of Health with collaborators from the colleges of engineering, medicine, and science at FAU. That project used an amputee’s movement and sensors that measured electrical signals to capture touch sensation and stimulate their damaged nerve cells.
This was their first approach to the problem of a lack of touch sensation and now with liquid metal sensors added to the project their goals feel closer than ever,
he said.
Engeberg chose liquid metal sensors because it’s a softer, stretchable material with a higher flexibility and it’s highly conductive, meaning it has the potential to pick up stronger sensations from the fingertips. The sensors, likewise, detect the speed of a moving object better than other sensors used on robotic hands, he continued. It’s also possible that the material used on an entire prosthetic hand or arm will give it a closer, more human-like touch.
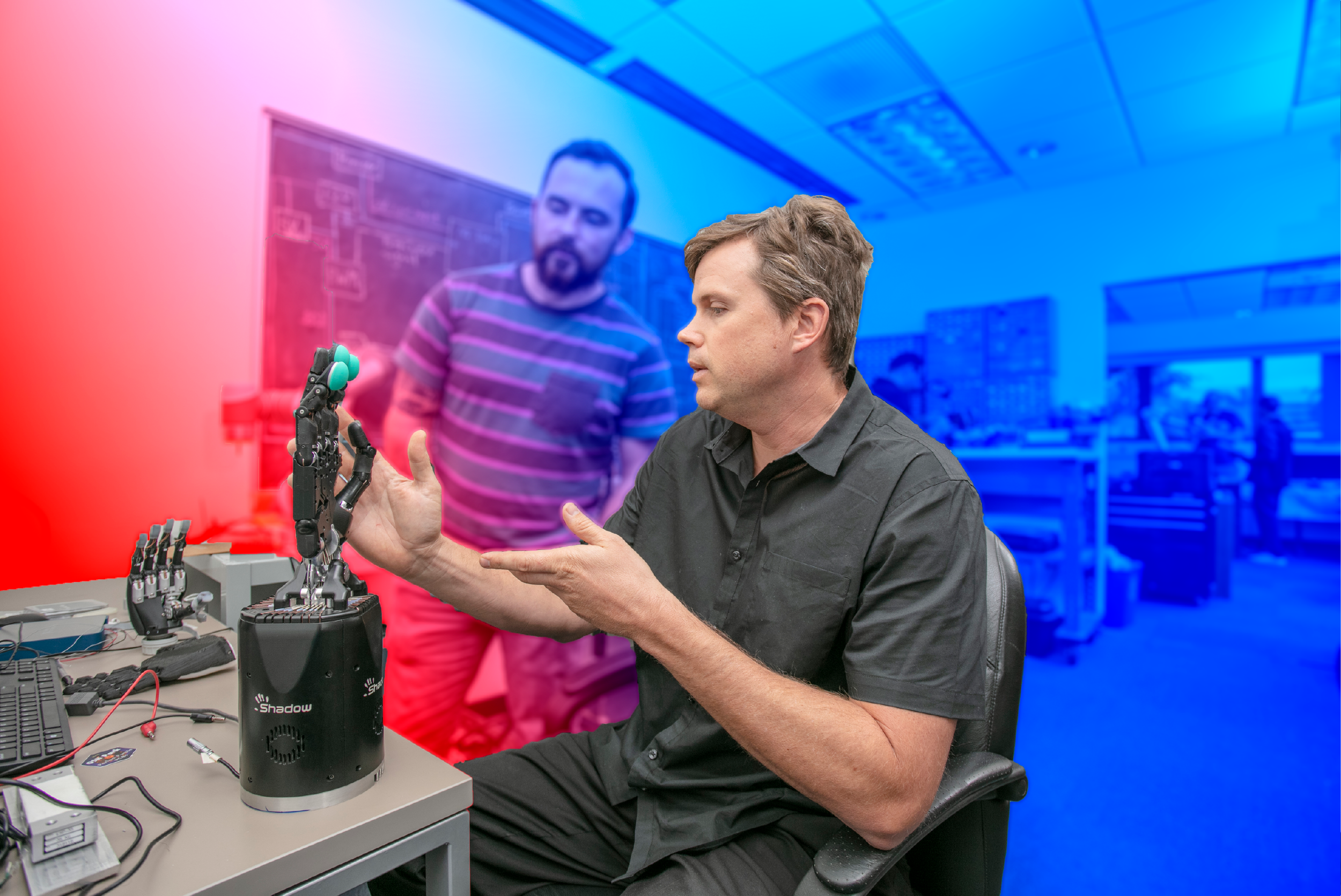
“If prosthetics could have a lighter softer touch, it’ll prevent amputees from abandoning their prosthetic hands altogether,” he said.
Recently, Engeberg tested the artificial sensations of touch with amputee participants and discovered so far, they’ve successfully distinguished multiple sensations of touch from multiple fingertips simultaneously, which is not possible with current prosthetic technology, he said.
“This is key to all the work we’ve worked so hard towards. I know there are so many other amputees who will benefit from better artificial limbs,” he said.
Engeberg and his team started the work with robotics in 2014. He created his first robotic AI hand that provides individual movement to a specific robotic finger. They discovered ways to mimic the flexion and extension behaviors of human fingers by training the AI finger to open and close the cap from a water bottle.
“Our goal is to get one step closer to helping improve an amputee’s quality of life with more natural prosthetic options that lets them feel and respond to their environment. Eventually every sensation on an artificial prosthetic should feel more natural,” Engeberg said. “It’s the future of AI.”
For his next step, Engeberg plans to design other in-depth textures that an AI prosthetic can determine, such as rocky surfaces or a smooth texture
“I’ve been working with prosthetics, mixing biology and applied engineering for more than 15 years,” Engeberg said. “It’s exciting to know this really is making
an impact.”